Milk powder blending and batching system
Milk powder blending and batching production line
Manual bag feeding (removing the outer packaging bag)-- Belt conveyor--Inner bag sterilization--Climbing conveyance--Automatic bag slitting--Other materials mixed into the weighing cylinder at the same time--Pulling mixer--Transition hopper--Storage hopper--Transportation--Sieving--Pipeline metal detector--Packaging machine
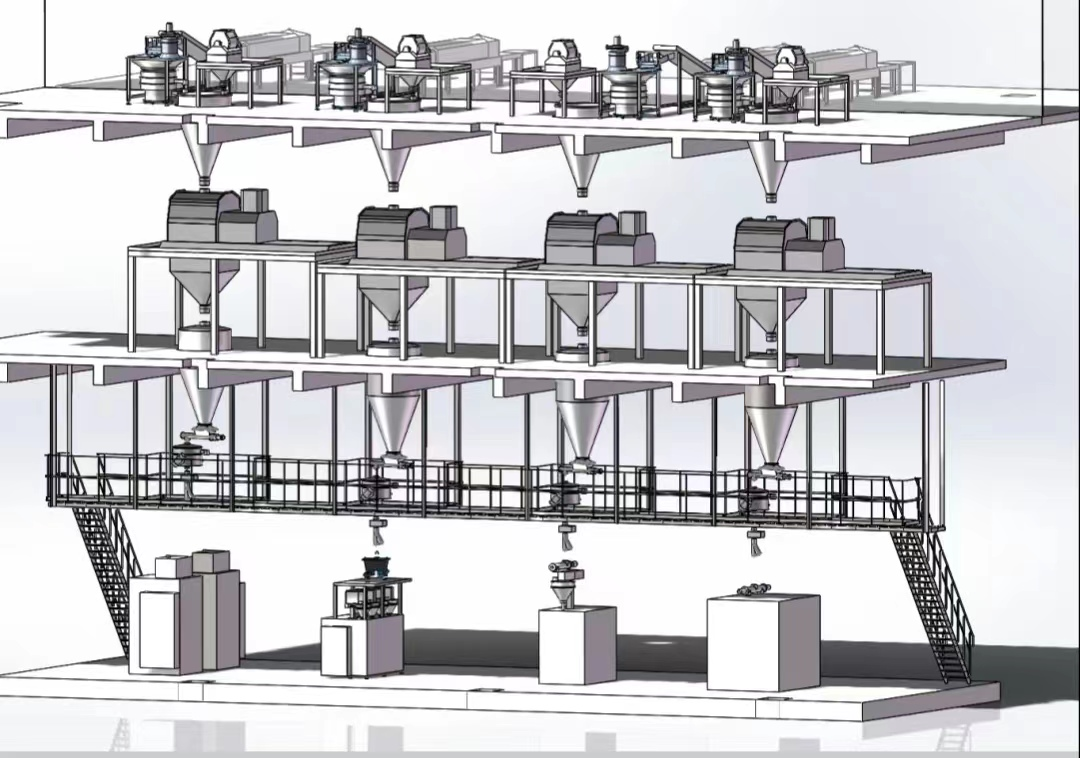
Can Milk Powder Blending and Batching Process
First step:Preprocessing
Because the raw milk of the dry blending method uses a large package of base powder (the base powder refers to cow milk or goat milk and its processed products (whey powder, whey protein powder, skimmed milk powder, whole milk powder, etc.) as the main Raw materials, adding part or not adding nutrients and other auxiliary materials, semi-finished products of infant formula milk powder produced by wet process), so in order to prevent the contamination of materials due to the contamination of the outer packaging during the mixing process, it is necessary to clean the raw materials at this stage .The outer packaging is vacuumed and peeled, and the inner packaging is vacuumed and sterilized before being sent to the next process.
In the preprocessing process, the operations are as follows:
- The large-pack base powder that has passed the inspection is subjected to the first dusting, the first peeling, and the second dusting step by step, and then sent to the tunnel for sterilization and transmission;
- At the same time, the raw materials such as various additives and nutrients that are ready to be added are dusted and sent to the sterilization tunnel for sterilization and transmission.
The picture below is the dust removal and sterilization operation of the outer packaging before peeling the base powder of the large package.
Second step:Blending
- The process of blending materials belongs to the process of cleaning. Strict sanitation and disinfection measures are required for workshop personnel and equipment, and the production environment must have constant parameter requirements, such as temperature, humidity, air pressure, and cleanliness.
- In terms of measurement, the requirements are very high, after all, it involves content issues:
1.Relevant records need to be established for the entire blending production and use to ensure traceability of product production information;
2.Before premixing, it is necessary to check the type and weight of materials according to the premixing formula to ensure accurate feeding;
3.Material formulas such as vitamins, trace elements or other nutritional elements must be entered and managed by special formula management personnel, and relevant personnel will review the formula to ensure that the weighing of the material is consistent with the formula requirements.
4.After ensuring that the material weighing is consistent with the formula requirements, it is necessary to identify the name, specification, date, etc. of the material after the weighing is completed
During the whole blending process, the operation steps are as follows
- The raw milk powder after the first step of pretreatment and sterilization is subjected to second peeling and metering;
- First blending of additives and nutrients
- Do the second blending of the raw milk powder after the second peeling and the additives and nutrients after the first blending;
- In order to ensure the uniformity of the mixing, the third mixing is carried out afterwards;
- And carry out sampling inspection on the milk powder after the third blending
- After passing the inspection, it enters the packaging stage through the vertical metal detector
Third Step: Packaging
The packaging stage also belongs to the cleaning operation part. In addition to meeting the requirements of the blending stage, the workshop must use a closed automatic can filling machine in order to effectively control artificial secondary pollution.
The packaging stage is relatively easy to understand. Generally speaking, the operation steps are as follows:
- The mixed powder that has passed the second step inspection is automatically filled and packed in cans with sterilized packaging materials
- After packaging, the cans are transported and coded, and the canned milk powder is randomly selected for inspection. The qualified cans are put into cartons and the boxes are marked with codes.
- Can milk powder that has completed all the above steps can enter the warehouse and wait for delivery
- Putting can milk powder into cartons
The following is a list of equipment used in the dry blending of canned infant milk powder:
- Ventilation equipment, including central air conditioning, air filters, ozone generators.
- Conveying equipment, including powder conveyors, belt conveyors , conveyor chains, sealed transfer windows, and elevators.
- Pretreatment equipment, including dust collector, vacuum cleaner, tunnel sterilizer.
- Blending equipment, including operating platform, shelf, three-dimensional blending machine, dry powder blending mixer
- Packaging equipment, automatic can filling machine, capping machine, inkjet printer, operating platform.
- Measuring equipment, electronic scales, air pressure gauges, automatic measuring can filling machines.
- Storage equipment, shelves, pallets, forklifts.
- Sanitary equipment, tool disinfection cabinet, washing machine, work clothes disinfection cabinet, air shower, ozone generator, alcohol sprayer,dust collector, dustbin, etc.
- Inspection equipment, analytical balance, oven, centrifuge, electric furnace, impurity filter, protein determination device, insolubility index stirrer, fume hood, dry and wet heat sterilizer, water bath, etc.